Framus


PERFECTION
The guitars from this German manufacturer are also called the 'Ferraris of guitars'. And anyone who takes a first look at this fine piece of work will immediately understand why: Framus offers high-quality guitars that are made with an eye for detail and the environment. Pure perfection, then!
Framus guitars is a relatively small-scale maker that now falls under Warwick (bass guitars), the brand of the son of Framus founder Fred Wilfer. Warwick operates climate neutrally and for the construction of Warwick/Framus guitars, 94% of the energy required is generated locally from wind and sun, while all other CO2 emissions are offset.
The story of Warwick and Framus began on January 1, 1946 with the founding of the "Fränkische Musikinstrumenterzeugung Fred Wilfer KG" in Erlangen/Bavaria.
Framus was one of the leading manufacturers of electric guitars in Europe between 1946 and the end of the 1970s. The company was founded by Fred Wilfer, the father of Hans-Peter Wilfer, who would found the Warwick company a few years later.
One of the most interesting chapters in the company's history is the relationship between Framus and its stars. The oldest and longest relationship between Framus and an outstanding guitar artist is with Billy Lorento (alias Bill Lawrence), which began in 1953. Shortly afterwards a very fruitful collaboration emerged with Attila Zoller, perhaps the most famous jazz guitarist of that time. For the idol of German rock'n'roll music, Peter Kraus, a new 4-string guitar was built by Framus in 1957, the "Peter-Kraus pop song guitar".
Framus also worked with John Lennon and Bill Wyman, bassist of the Rolling Stones, who signed a 3-year endorsement contract.
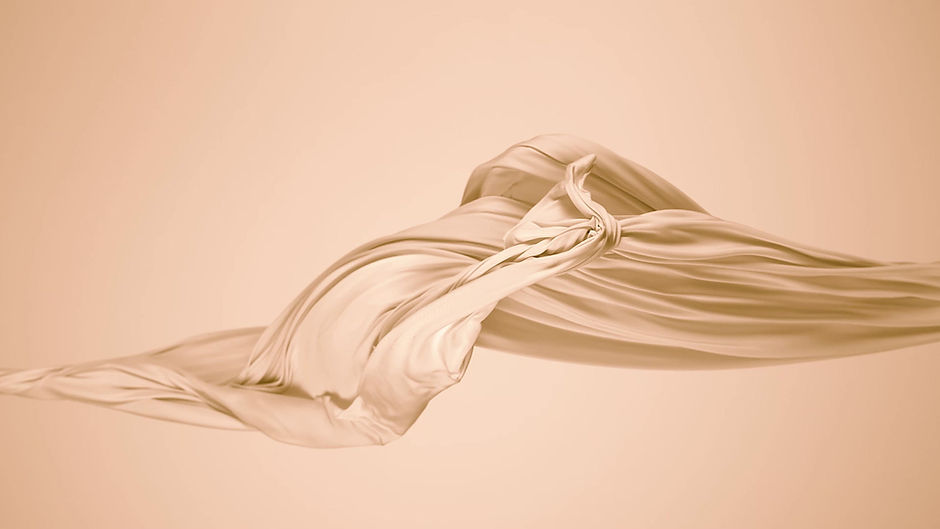
DIFFERENT
MODELS
The brand has no fewer than four different lines for you as a guitarist. The D-Series is a line that is manufactured in China and receives a final check in Germany.
The Teambuilt line, on the other hand, is built entirely in the Framus Custom Shop in Germany. The Masterbuilt is a line that we can only describe as the handmade crème de la crème: think of the best woods and hardware available and all built by the best Masterluthiers from Framus.
Finally, they have the Custom Shop. You can put together your dream guitar together with us and Framus. Completely put together your own wood types, pick-ups and other hardware, finish, etc. Have the ultimate guitar built once in your life. If you can dream it, Framus can build it.
The perfect fret
There is just a little more technology behind the production of the instruments from the Teambuilt and Masterbuilt line. All guitars from these lines have the Invisible Fretwork Technology (IFT). What does this mean? First, frets are installed and finished with precision down to a hundredth of a millimeter, with consistent quality. In addition, the fret slots are not cut across the entire fingerboard, as is done by most manufacturers. Two millimeters of wood are left 'open' on both sides, creating a kind of U-profile. This makes the neck of your guitar more resistant to possible twisting and vibrations are better transmitted.
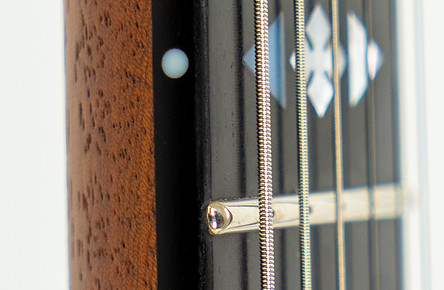
Star looks
The fact that Framus delivers top quality has not gone unnoticed by the world's biggest stars. Framus' oldest and longest 'star relationship' is with Billy Lorento (Bill Lawrence) in 1953. Shortly afterwards a very fruitful collaboration arose with Attila Zoller, perhaps the most famous jazz guitarist of that time.
Framus continues to work closely with various artists, such as Devin Townsend, William Duvall of Alice in Chains, Guilherme Miranda of Entombed and of course Marco Hietala of Nightwish. Did you know that we also have a love child from Framus and a star in our home? The Framus D-Series Idolmaker Solid Black Satin was developed with none other than Stevie Salas!
The Teambuilt and Masterbuilt lines are also adjusted with the 'spot technique', an advanced and accurate measuring and trimming technique. The guitars are measured at every possible playing position. The pressure is accurately calculated by simulating the resistance of the guitar strings and taking into account the arch of the neck.
Then, in the trimming process, each fret is worked individually, based on the previous measurements. The fret radius is retained even after the milling process. The result is a flat string position, perfectly rounded fret crowns, improved intonation and great playing comfort. In short: say goodbye to fret buzz, even at the lowest actions!
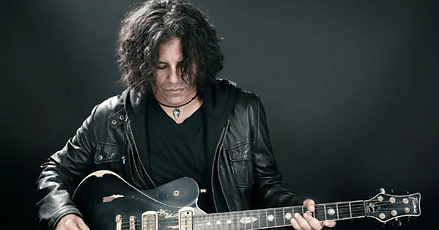
Sustainability
Framus is a relatively small-scale maker that now falls under Warwick, the brand of the son of Framus founder Fred Wilfer. Nice to know: Warwick operates climate neutrally! For the construction of Warwick/Framus guitars, 94% of the energy required is generated locally from wind and sun, while all other CO2 emissions are offset. That makes us happy! :)
Framus
94% CO2 neutral
